با توجه به ساخت و سازهای نوین شهری و اهمیت اجرای ساختمانهای بلندمرتبه و سنگین و نیز استفاده هر چه بیشتر از زمینهای مستعد سرمایهگذاریو جذب گردشگر که در پارهای اوقات منجر به اجرای سازه در زمینهای سست و خاکهای نامناسب میگرد، لزوم بکارگیری روشهای نوین ژئوتکنیکی جهت تقویت مکانیکی خاکهای موجود که ضرورتهایی چون سرعت بالای اجرا، هزینههای معقول، عدم ایجاد مزاحمت به املاک مجاور، عدم توقف در ترافیک جادهای و …را نیز مدنظر قرار داده باشد، نمود بارزی پیدا میکند.سیستم ریزشمع (Micropile) و فنداسیونهای ریزشمعی از روشهای روز ژئوتکنیکی است که گستره کاربرد آن در تمامی دنیا بالاخص کشورهای پیشرفته غیرقابل انکار میباشد. از سوی دیگر به دلیل جوان بودن علم ژئوتکنیک و روشهای ژئوتکنیکی در ایران و نبود آیین نامهها و دستورالعملهای اجرایی و روشهای عقد قرارداد مدون، گاها شاهد برخی بدعتها و نوآوریهای نابجا در عرصه روشهای اجرایی میباشیم، که خود منجر به مشکلات متعاقب بین کارفرما و پیمانکار میگردد. بروز این مشکلات باعث طولانی شدن پروژه و طرح دعوی از سوی طرفین قرارداد میگردد و نهایتا کارفرما نسبت به روشهای نوین ژئوتکنیکی مایوس شده و این صلب اعتماد منجر به تمایل و سوق کارفرما به سمت روشهای سنتی میگردد.مسلما بومی سازی چنین سیستمهایی مستلزم پژوهشها و مطالعات دانشگاهی و آزمایشگاهی فراوان و راهنمایی اساتید صاحب نظر در این زمینه میباشد که خوشبختانه در سالهای اخیر اقدامات مثبتی در این راستا در میهن عزیزمان، ایران اسلامی صورت گرفته است.
ریزشمعها در اوایل دهه 1950 در ایتالیا، برای تقویت پی بناهای تاریخی و یادبودهایی که با گذشت زمان و بویژه در طی جنگ جهانی دوم در معرض آسیب و تخریب قرار گرفته بودند، ظهور کردند. در آن زمان به یک سیستم مطمئن برای نگهداری بارها و وزن سازهها با کمترین جابجایی، قابل اجرا در فضاهای با دسترسی محدود با کمترین آسیب و خسارت وارده بر سازههای موجود، نیاز بود. یک پیمانکار ایتالیایی به نام Fondedile، روش “Palo radice” یا “روت پایل” ها را برای تقویت پی سازهها پیشنهاد داد. Palo radice یک شمع با قطر کوچک میباشد که در محل، حفاری و اجرا شده و پس از قراردادن آرماتور سبک، تزریق میشد. اگرچه فولاد پس از جنگ در اروپا کم تولید میشد، اما نیروی کارف ارزان قیمت و فراوان بود و اغلب آنهها نیز قابلیتهای فنی بالایی داشتند. چنین شرایطی بستر توسعه روت پایلهای کم آرماتور را مهیا نمود که عمدتا توسط پیمانکاران طراحی و اجرا میشد. آزمایشهای بارگذاری بر روی این روتپایلها، ظرفیتهای باربری فراتر از 400 کیلونیوتن را ثبت کرد، اگرچه برای ظرفیت باربری اسمی طراحی بر پایه روشهای طراحی شمعهای مرسوم با روشهای حفاری همان زمان، چیزی کمتر از 100 کیلونیوتن در نظر گرفته شده بود. آزمایشهای تمام مقیاس، تقریبا با هزینههای نسبتا پایین اجرا میشدند.در طی این آزمایشها، هیچ گونه گسیختگی در ناحیه پیوند خاک-دوغاب ثبت نشد. استفاده از روت پایلها در طی دهه 1950 در ایتالیا توسعه یافت. آقای Fondedile این تکنیک را برای تقویت پی چندین سازه تاریخی به سال 1962 در انگلستان پیشنهاد داد و به سال 1965 این روش در فنداسیون پروژههای راه و ترابری آلمان مورد استفاده قرار گرفت. در همان زمان، بنا به دلایل خاص مالکیت زبانی، “ریزشمع” جایگزین “روت پایل” شد. در ابتدا کاربرد اصلی ریزشمع برای تقویت پی سازهها در محیطهای شهری بود. با شروع سال 1957، تقاضای مضاعف مهندسی منجر به پیدایش سیستم “raticoli di pali radice” (ریزشمع مشبک) گردید. این سیستم شامل چندین ریزشمع عمودی و مایل که در یک شبکه سه بعدی در هم قفل شده باشند، میگردید. این سیستم منجر به ایجاد یک سازه محصور شده، مرکب از خاک-شمع میشد. ریزشمع مشبک، برای پایدارسازی شیروانیها، تقویت دیوارهای ساحلی و بندری، حفاظت از سازههای مدفون و سایر موارد نگهداری و تقویت خاکها و سازهها و مقاوم سازی زمین به کار گرفته شد.
سیستم ریزشمع در سوئیس و آلمان توسعه یافت و خیلی زود در خاور دور تبدیل به بازار اصلی این فنآوری شد. وفور کارگران نسبتا ارزان، کمبود فولاد و نیاز مبرم به ترمیم و بازسازی محیطهای شهری، همگی موجب افزایش استفاده از ریزشمعها در اروپا گردید. بالعکس، رشد تاخیری و آرام استفاده از ریزشمعها در شمال امریکا، بازتابی از فراوانی فولاد ارزان قیمت، هزینههای نسبتا بالای کارگر، و اجرای پروژههای بزرگ در مناطق برون شهری بود. چنین شرایطی موجب توسعه تکنیک شمعهای جابجایی گردید که با استفاده از دفترچه مشخصات تجویزی اجرا میشدند و از تکنولوژی پایینتری نسبت به ریزشمعها برخوردار بودند. امروزه هزینههای اجرا در سراسر جهان تقریبا مشابه هم هستند و رشد تقاضا برای ریزشمع ادامه دارد، بویژه در بین پیمانکاران ژئوتکنیکی که توانایی ساخت و طراحی را دارا میباشند.
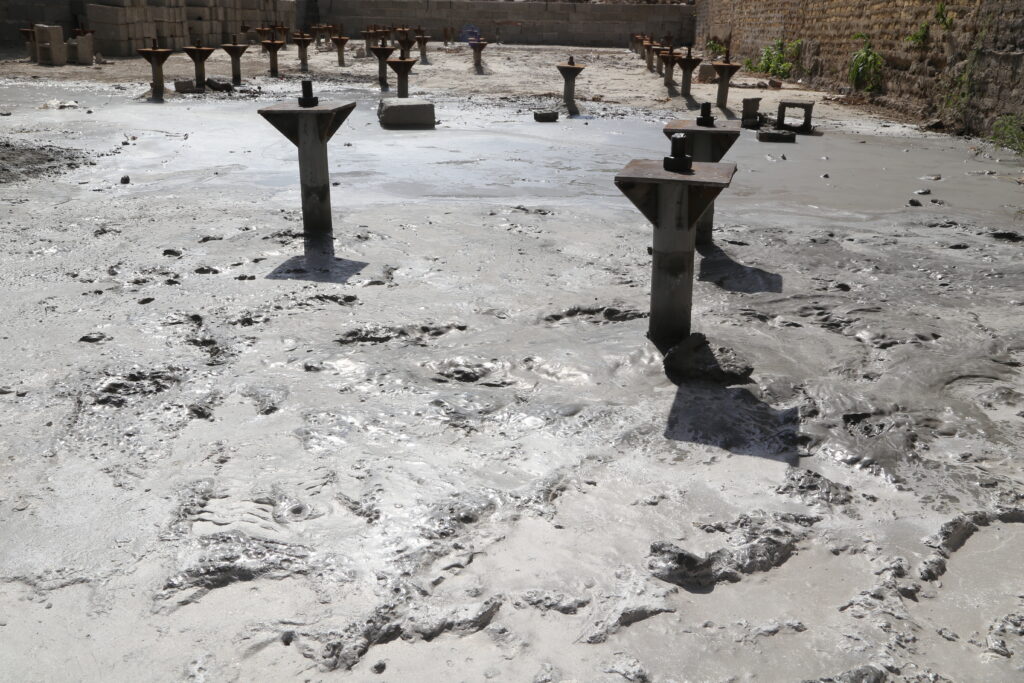
طبقه بندی میکروپایل به لحاظ اجرا
به طور کلی، روش تزریق در حین اجرا، حساسترین پارامتر موثر بر ظرفیت باربری مجموعه زمین-دوغاب میباشد. ظرفیت باربری مجموعه زمین دوغاب به طور مستقیم با تغییر روش تزریق، تغییر میکند. بخش دوم طبقه بندی ریزشمعها شامل یک حرف مشخص (از A تا D) میباشد که بر اساس روش تزریق و فشار تزریق مورد استفاده در حین اجرا انتخاب میشود. استفاده از غلافگذاری و آرماتور این طبقه بندی را ریزتر میکند.
نوع A: این طبقه بندی بیانگر یک تزریق ثقلی (بدون فشار پمپ) میباشد. از آنجا که ستون تزریق تحت فشار نمیباشد، هم میتوان از ملات ماسه-سیمان، و هم از دوغاب سیمان استفاده نمود. به منظور افزایش ظرفیت کششی، میتوان قطر گمانه شمع را بیشتر نمود. اگرچه این تکنیک رایج نبوده و در سایر انواع شمعها مورد استفاده قرار نمیگیرد.
نوع B:این نوع دلالت بر تزریق تحت فشار دوغاب سیمان به درون گمانه دارد، در حالیکه غلاف اولیه حفاری، بیرون کشیده میشود. فشار تزریق معمولا بین 0.5 تا 1 مگاپاسکال متغیر است و محدودهای نگه داشته میشود که در خاک اطراف ترکهای هیدرولیکی ایجاد نگردد و از طرفی پوشش و درزگیری لازم برای جلوگیری از ریزش جداره در حین بیرون کشیدن غلاف، حدالامکان تامین گردد.
نوع C: این بیانگر یک پروسه تزریق دو مرحلهای میباشد:1) دوغاب سیمان تحت اثر وزن خود به مانند نوع A تزریق میگردد 2) پس از سخت شدن تزریق اولیه (بعد از تقریبا 15 تا 25 دقیقه) تزریقی مشابه، ولی اینبار از طریق یک لوله تزریق غلافدار بدون استفاده از پکر (در سطح مشترک ناحیه تزریق) تحت فشاری حداقل 1 مگاپاسکال صورت میگیرد. به نظر میرسد که این نوع شمع فقط در فرانسه استفاده میگردد و به نوع IGU اشاره دارد.
نوع D: این روش به یک پروسه تزریق دو بخشی مشابه نوع C، البته با اصلاحاتی در مرحله دوم اشاره دارد. در مرحله اول دوغاب سیمان همانند نوع A و C به صورت ثقلی تزریق میگردد و شاید همانند نوع B تحت فشار صورت گیرد. بعد از سخت شدن تزریق اولیه، دوغاب ثانویه از تزریق یک لوله تزریق غلافدار تحت فشار 2 تا 8 مگاپاسکال تزریق میشود. ممکن است از یک پکر نیز استفاده میشود، تا در صورت لزوم حرکت افقی غلاف محدود گردد. این نوع شمع به طور رایج در تمام جهان استفاده میگردد و در فرانسه به نام IRS شناخته میشود.
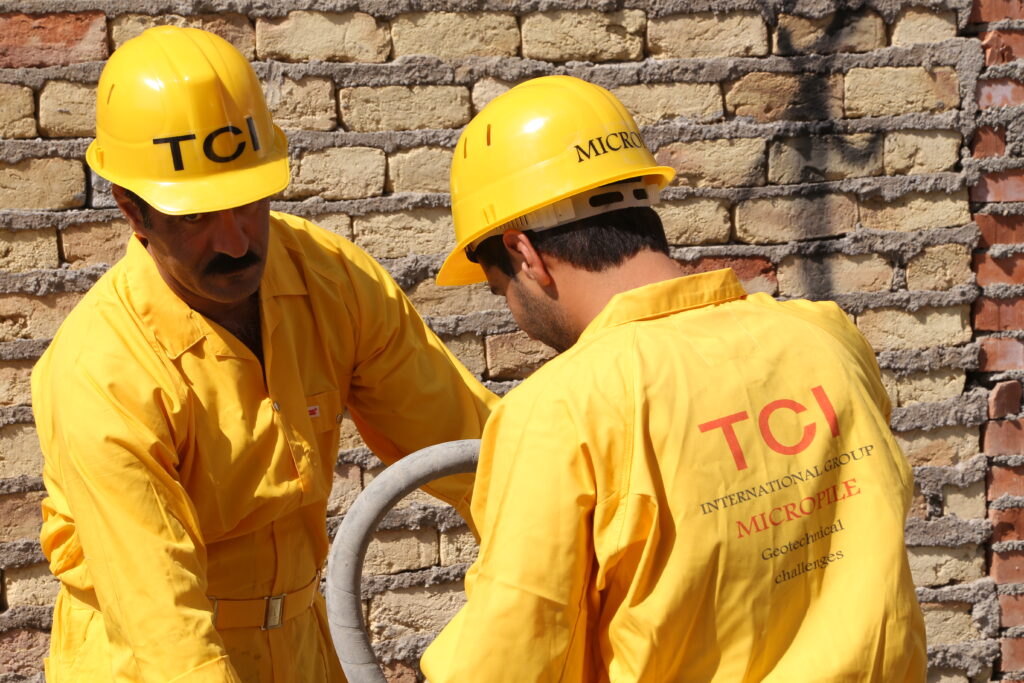
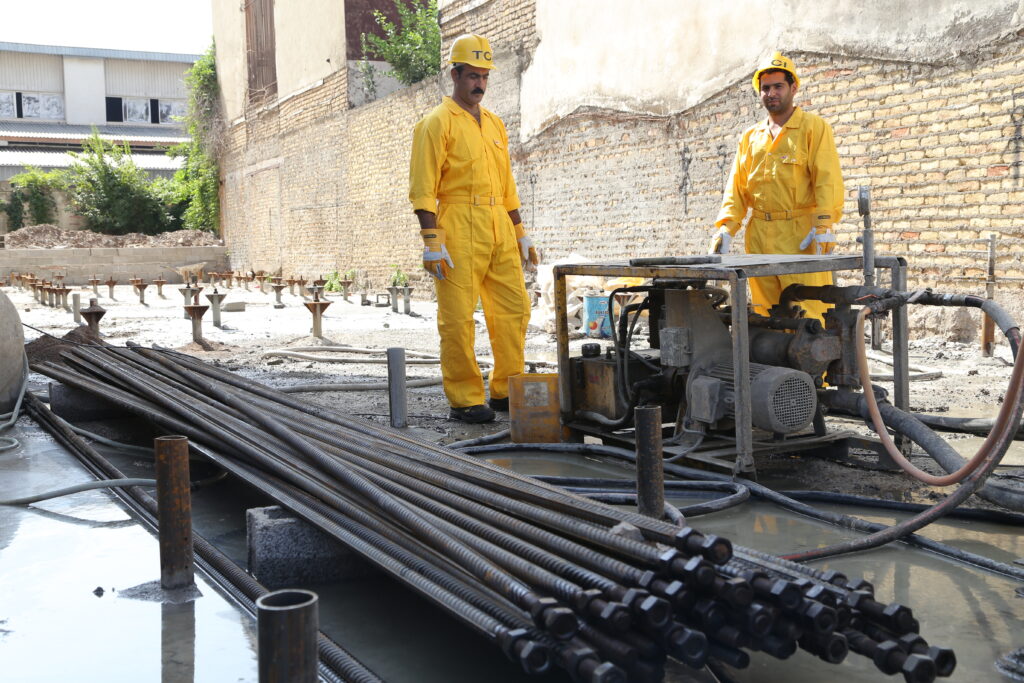
تقویت فنداسیون سازههای موجود
ریز شمعها اساسا ، به منظور تقویت فنداسیون سازههای موجود توسع هیافتند. تقویت پی سازههای موجود ممکن است برای مقاصد بسیاری اجرا گردد:
- برای جلوگیری و ممانعت از جابجایی سازه
- برای بالا بردن ظرفیت باربری سازههای موجود
- برای تقویت فنداسیونهای ضعیف و در حال زوال
- برای محافظت در مقابل آب شستگی پیهای فرسایش پذیر
- برای بالا آوردن سطح فنداسیونهای نشست کرده تا تراز ارتفاعی اولیه خود
- برای انتقال بارها تا لایههای عمیقتر و مستحکمتر
ریزشمعها را میتوان از میان سازههای موجود اجرا نمود و بدون نیاز به کلاهکهای شمعی ( دال بتنی) جدید یک ارتباط مستقیم با لایه مستحکم زیرین تامین کرد، در حالیکه همزمان با این کار سازه از داخل تقویت میشود. ریزشمعها را میتوان بدون هیچ گونه کاهش در ظرفیت باربری فنداسیونهای موجود اجرا نمود.
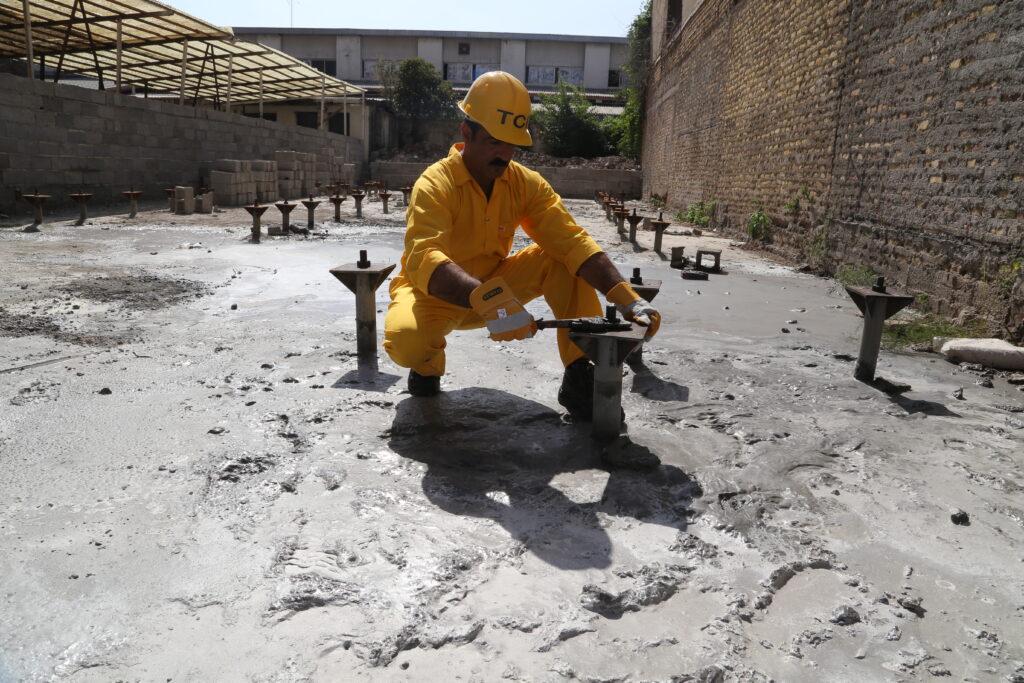
جایجایی و نشست سازه میتواند بوسیله تغییر در عواملی همچون، تراکم زمین زیر فنداسیون موجود، تخلیه آب زیرزمینی، نوسان سطح آب زیرزمینی، زوال فنداسیونهای موجود و فالیتهایی از قبیل حفر تونل و گودبرداریهای عمیق در مجاورت سازه ایجاد شود. اجرای ریزشمعها در لایههای عمیقتر و مستحکمتر، جابجاییهای سازهای را کاهش داده و موجب تامین تکیهگاهی مستحکم برای فنداسیون میگردد. افزایش ظرفیت باربری فنداسیون موجود ممکن است به چند دلیل لازم باشد. ممکن است در اثر توسعه سازههای مجاور، افزایش میزان و بزرگی بارهای اعمالی یا اضافه شدن ماشینهای مولد ارتعاش در محل، بارهای ارتعاشی، جانبی و عمودی بیشتری به سازه وارد گردد.
مقاوم سازی لرزهای
ریزشمعها به طور فزاینده برای مقاوم سازی لرزهای بزرگراهی، استفاده میشوند. با وجود یک یا چند مورد از محدویتهای زیر، ریزشمعها میتوانند به لحاظ اقتصادی برای مقاوم سازی فنداسیون پلها میسر باشند:
- محدودیت در توسعه و بزرگی پیها
- محدودیتهای ارتعاشی و آلودگی صوتی
- ارتفاع کم و فضای باز ناکافی
- ورودیهای دشوار
- وجود بار محوری کششی و فشاری زیاد
- شرایط سخت و دشوار برای حفاری و راندن شمعهای جابجایی
- مناطقی دارای خاک با ریسک بالا
ریزشمعها ظرفیت کششی و فشاری تقریبا برابری را از خود نشان میدهند، به همین دلیل، تعداد المانهای پشتیبانی فنداسیون اضافی لازم به حد بهینه خود میرسد.
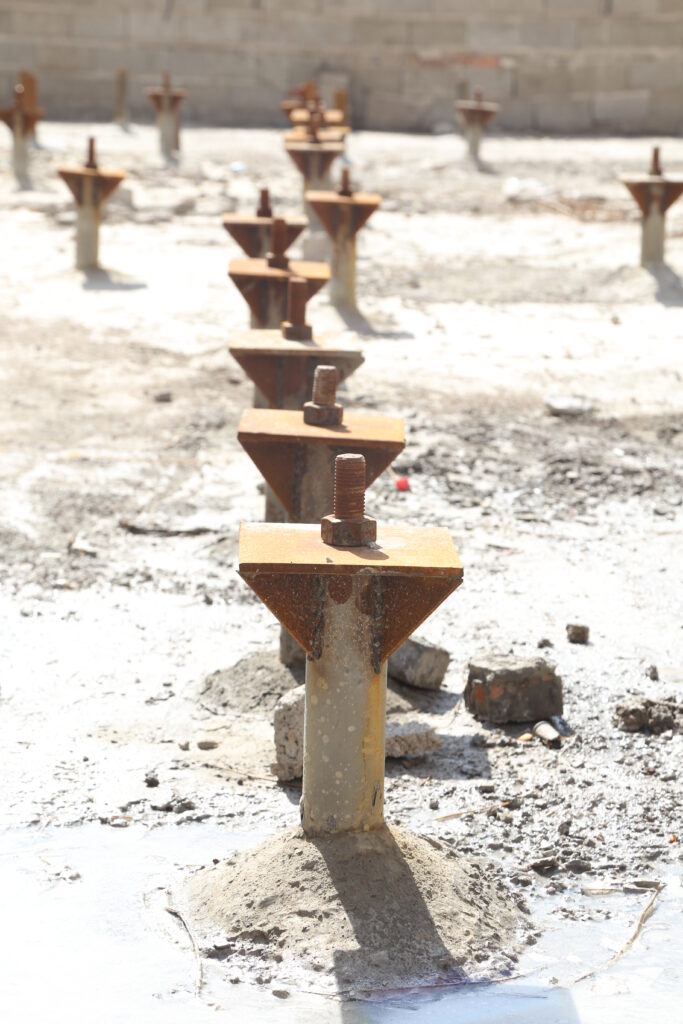
عوامل موثر در انتخاب ریزشمع
چندین عامل در انتخاب ریزشمعها برای تقویت فنداسیون سازهها و پایدارسازی شیروانیها تاثیرگذار میباشند:
- ملاحظات فیزیکی شامل محدودیت دسترسی، مناطق دور افتاده، مجاورت شمعهای نزدیک به هم برای سازههای موجود
- شرایط زیرزمینی شامل شرایط نامناسب زمین، پتانسیل زمین برای شروع روانگرایی در طی راندن شمعهای درجا
- شرایط محیطی شامل مناطق حساس به آلودگی صوتی و ارتعاش، خاکهای خطر آفرین یا آلوده
- سازههای موجود شامل محدودیتهای اجرای ریزشمع، مسائل اقتصادی
ملاحظات فیزیکی
تجهیزات حفاری و تزریق مورد نیاز برای اجرای ریزشمعها نسبتا کوچک میباشد و میتوان آنها را به فضاهایی که دسترسی به آنها مشکل است حمل کرد. در حالیکه نمیتوان تجهیزات اجرا و نصب شمعهای مرسوم را به این مکانها وارد نمود. ریزشمعها را میتوان در فاصله چند میلیمتری از دیوارها یا فنداسیونهای موجود اجرا نمود، که این خود تامین کننده فضای باز برای سرمته و ناحیه کار ایمن میباشد، در حالیکه شمعها چنین قابلیتی ندارند. نصب و اجرای ریزشمعها تحت تاثیر خطوط انتقال برق بالاسری یا سایر موانع مرسوم در سیستم اجرا و نصب شمعها نمیباشد. تجهیزات لازم را میتوان به بالای شیروانیها و فضاهای پرت و دور افتاده حمل کرد. در ضمن اگر روشهای حفر و تزریق مناسب به کار گرفته شوند، پروسههای حفاری و تزریق در اجرای ریزشمعها هیچ آسیبی به سازههای مجاور موجود وارد نمیآورد و بر شرایط زمین مجاور تاثیر نمیگذارد.
شرایط زیرسطحی
ریزشمعها را میتوان در مناطقی با شرایط ژئوتکنیکی غیرقابل پیشبینی، متغیر و سخت مانند زمینهایی لاشه سنگی و تخته سنگی، پر از تاسیسات مدفون و زبالهها و پسماندهای متفرقه و لنزهای غیرمعمول از مصالخ ضعیف و مستحکم اجرا و نصب نمود. رسهای نرم، ماسههای روان و سطح بالای آب زیرزمینی که برای سیستم حفر میل چاهها مساعد نیستند، کمترین تاثیر نامساعد را بر نصب و اجرای ریزشمعها دارند.
شرایط محیطی
ریزشمعها را میتوان در خاکهای خطرآفرین و آلوده اجرا نمود. قطر کوچه آنها منجر به ایجاد ضایعات و اتلاف کمتری نسبت به شمعهای درجا مرسوم میگردد و تلفات شستگی در سطح زمین را میتوان براحتی از طریق متمرکز سازی یا استفاده از گودالهای سطحی خطی کنترل نمود. این عوامل به طور چشمگیری پتانسیل آلودگی سطحی و هزینههای جابجایی را کاهش میدهد. مخلوط دوغاب سیمان را میتوان برای مقاومت در برابر حملههای شیمیایی آبهای زیرزمینی و خاک طراحی کرد. در طرح مخلوط دوغاب سیمان یک ترکیب ویژه را میتوان برای کاهش و جلوگیری از زوال ناشی از محیطهای اسیدی و خورنده در نظر گرفت. ریزشمع ها را میتوان در مناطق و محیطها حساس، من جمله مناطقی با ساختار طبیعی شکننده اجرا نمود. تجهیزات اجرا و نصب به بزرگی و سنگینی تجهیزات حفاری و راندن شمعهای مرسوم نمیباشد و میتوان از آنها در مناطق باتلاقی یا سایر مناطق با خاک سطحی خیس و نرم استفاده نمود که کمترین تاثیر را بر روی محیط میگذارد. در مناطقی با دسترسی محدود تجهیزات حفاری قابل حمل و نقل بسیار استفاده میگردد.اجرای ریزشمعها سر و صدای کم و ارتعاش کمی را نسبت به تکنیکهای اجرای شمعهای مرسوم، بویژه راندن شمعهای درجا، ایجاد مینماید. ارتعاش ناشی از راندن شمع بر خاک تاثیر گذاشته و میتواند از میان خاک عبور کرده و به سازههای مجاور برسد. استفاده از ریزشمعها در محیطهای شهری قدیمی و محیطهای صنعتی-تولیدی، میتواند از پتانسیل تخریب و آسیب به سازهها و تجهیزات حساس مجاور جلوگیری کند. ریزشمعها را میتوان در مناطقی که سفره آب آلودهای بر روی یک لایه مقاوم قرار گرفته است، اجرا نمود. بر خلاف شمعهای درجا که ممکن است یک کانال عمودی برای انتقال آلودگی ایجاد کنند، ریزشمعها را میتوان به روشی اجرا نمود که از گسترش آلودگی سفره آب زیرین ممانعت نماید.
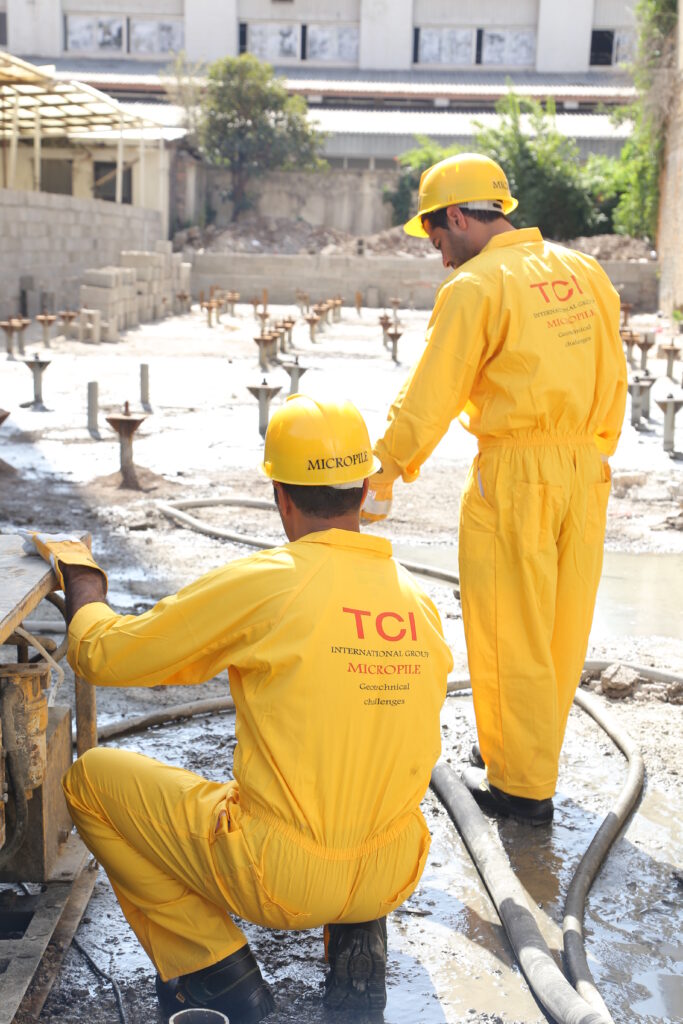
تطبیق سازههای موجود
ریزشمعها را میتوان در داخل کلاهک دال بتنی شمع و به شمعهای موجود اضافه نمود، بنابراین نیاز به افزایش ابعاد پی از بین میرود. این موضوع موجب تامین مقاومت فشاری، کششی و خمشی اضافی وابسته به افزایش بارهای سازهای میگردد. اغلب اوقات تاسیسات مجاور و یا سازهها مانع از افزایش ابعاد کلاهکهای شمعهای موجود میشوند. بنابراین سیستم اجرای شمع سنتی بیش از پیش از دور خارج میشود.
تزریق
همانطور که در قبل گفته شد، عملیات تزریق تاثیر مهمی بر ظرفیت باربری ریزشمع دارد و اساسی ترین تقسیمبندی ریزشمعها به لحاظ ساخت و اجرا نیز مبتنی بر روش تزریق میباشد. جزئیات هر کدام از انواع عملیاتهای تزریق گاهی اوقات در اقصی نقاط جهان بسته به مبدا اجرا و کیفیت منابع محلی دست خوش تغییر میشود. اما با ملاحظات کلی میتوان چنین گفت که:
- دوغاب سیمان برای تامین مقاومت و استقامت بالا طراحی میشودف اما همچنین بایستی قابلیت پمپ شدن را نیز داشته باشند.
- به منظور کاستن از خطر خوردگی آرماتورها ، دوغاب سیمان باید با آب قابل شرب تهیه گردد.
- بیشتر از مخلوط آب و سیمان استفاده میشود، اگرچه در برخی کشورهای خاص ماسه یک افزودنی رایج میباشد. بنتونیت در مخلوط اولیه همراه با احتیاط زیاد استفاده میگردد، درحالیکه افزودنیها صرفا محدود به مواردی میشوند که قابلیت پمپاژ در میافتهای طولانی و یا در آب و هوای گرم را ارتقا دهند.
- باید مقاومت فشاری طرح، معادل 28 تا 35 مگاپاسکال را با یک پروسه تهیه و تولید مناسب دوغاب سیمان بدست آورد.
اهمیت حیاتی روش اجرای تزریق با این حقیقت مشخص میشود که دوغاب تزریق شده بایستی اهداف زیر را تامین کند:
- بایستی بارهای اعمالی بین آرماتورها و خاک اطرافش را انتقال دهد.
- دوغاب بخشی از مقطع عرضی شمع، که متحمل بارها میباشد را تشکیل میدهد.
- بایستی آرماتورهای فولادی را از خوردگی حفظ کند.
- اثرات دوغاب ممکن است بواسطه تراوش، تراکم و یا شکاف و ترک خوردگی، از محدوده گمانه حفاری شده فراتر رود.
بنابراین دوغاب سیمان بایستی خواص لازم سیالیت، مقاومت، استحکام و دوامپذیری را دارا باشد. درک اشتباه از شرط سیالیت دوغاب میتواند منجر به افزایش آب گردد، که این موضوع تاثیر سوء بر سه خاصیت دیگر مذکور دارد. در بین عواملی که بر سیالیت دوغاب و سایر خواص آن تاثیر دارند، نسبت آب به سیمان غالب میباشد. برای ساخت شمع سالم ضرورری است که پس از تکمیل عملیات تزریق، در هیچ یک از قسمتهای مختلف شمع که جهت تحمل بار یا حفاظت از خوردگی به کار میرود، کمبود عمده و قابل توجهی از دوغاب سیمان وجود نداشته باشد. مشکلات ناشی از نقصان دوغاب ممکن است استفاده از یک ماده پرکننده مثل ماسه را برای بستن لایههای نفوذپذیر الزامی نماید، یا ممکن است لازم باشد که گمانه را تزریق کرده و مجددا پس از گیرش تزریق اولیه، حفاری کرده دوباره تزریق را انجام دهیم.
اختلاط دوغاب
در ابتدا، حجم معینی از آب در میکسر ریخته میشود، در ادامه سیمان و سپس مصالح دانهای یا پرکننده اضافه میگردد. عمما توصیه شده است که دوغاب بایستی حداقل به مدت دو دقیقه مخلوط گشته و سپس قبل از پمپ شدن به درون شمع، تحت یک تلاطم آرام و پیوسته درون میکسر ثانویه نگهداری شود. تنها در مصارف زیاد، مثلا در مواردی که انتظار میرود قطعات بزرگ استثنایی آماده گردد، نیاز به مخزن ذخیره دوغاب میباشد. دوغاب بایستی، در طی حداکثر زمان خاصی پس از اختلاط تزریق شود. با توجه به آنکه این زمان “کارایی ایمن” به عوامل متعددی وابسته است، لذا این زمان بایستی بر اساس آزمایشهای برجا تعیین شود. اما عموما نباید فراتر از یک ساعت رود.
آب نیز بوسیله یک تانکر مدرج یا جریان سنج، به مجموعه درون میکسر اضافه میشود. سیمان معمولا بر اساس وزن، یا به صورت سیمان کیسهای و یا سیمان ذخیره شده در سیلو به مجموعه اضافه میشود. ماسه یا مصالح پرکننده نیز بر اساس وزن بوسیله کیسههای از پیش اندازهگیری شده یا به طور رایج ، با استفاده از یک گیج باکس که پیشاپیش کنترل و وزن شده است به مجموعه اضافه میشوند. در مورد مصالح فلهای برای کنترل کیفیت اجزای اضافه شده به مخلوط، بایستی روشهایی اندیشیده شود.
ظرفیت ژئوتکنیکی مجموعه خاک-دوغاب
بدلیل عوامل زیر، معمولا در طراحیها فرض میشود که بار ریزشمعها بدون هیچ گونه مشارکت ظرفیت باربری نوک و صرفا از طریق اصطکاک جلدی بین خاک-دوغاب به زمین انتقال مییابد:
- ظرفیت بالای مجموعه خاک-دوغاب که میتواند با اجرای متوالی مراحل ساخت ریزشمع بدست آید. این ظرفیت برای ریزشمعهای با قطر معمول ناحیه پیوند (300-150 میلیمتر) در خاکهای دانهای متراکم به مقدار نهایی فراتر از 365 کیلونیوتن بر هر متر از طول پیوند و در سنگهای مستحکم فراتر از 750 کیلونیوتن بر هر متر طول پیوند میرسد.
- سطح جانبی (اصطکاک جلدی) بطور قابل توجهی بیشتر از مساحت انتهای ریزشمع میباشد. برای شمعی با قطر 200 میلیمتر و طول 6 متر، سطح جانبی 120 برابر بیشتر از سطح مقطع انتهای شمع میباشد.
- حرکت مورد نیاز شمع جهت بسیج مقاومت اصطکاکی بطور قابل ملاحظهای کمتر از مقدار مشابه بسیج مقاومت انتهای شمع میباشد.
وابستگی شمعها به اصطکاک جلدی به لحاظ ژئوتکنیکی در کشش و فشار یکسان در نظر گرفته میشود. این یک فرض طراحی رایج در تعیین طول پیوند، در یک شمع فشاری-کششی میباشد.
ابزارسنجی آزمایشهای صورت گرفتهبر روی مهارهای Tieback و ریزشمعها نشان داده استکه بویژه در خاکهای متراکم و سخت و سنگهای مستحکم، نرخ انتقال بار به زمین در انتهای طول پیوند بیشتر است. این موضوع در زمان محاسبه نشستهای مورد انتظار شمع، بیشتر مد نظر قرار میگیرد. طبق مشاهدات عملی میتوان گفت که، تمرکز عکسالعمل بارگذاری اعمال شده در بخشهای فوقانی طول پیوند طور موثر طول تغییرشکل (الاستیک) شمع را کاهش داده و مقدار نشست را بویژه در خاکهای سخت و سنگها کاهش میدهد. در حالیکه استفاده از ریزشمعها به سرعت توسعه مییابد، طراحی ژئوتکنیکی کنونی اساسا مبتنی بر تجربیات و تحقیقات در میل چاههای حفر شده، میخکوبی خاک و مهارهای Tieback میباشد.
گروه ریزشمعها تحت بارگذاری محوری
طرح سیستمهای نگهبان فونداسیون با ریزشمعهای ترکیبی ممکن است نیازمند اجرای گروهی از شمعها در کنار هم باشد. با سیستمهای مرسوم شمع، بسته به نوع شمع، روش اجرا، و شرایط خاک، تحت میزان بار متوسط یکسان برای هر شمع در گروه، ظرفیت باربری گروه شمع بطور قابل توجهی کمتر از مجموع ظرفیت شمعهای منفرد و نشستهای گروه شمع بزرگتر از نشست شمع منفرد میباشد. این تاثیر برای شمعهای حفاری شده بسیار بیشتر است، جاییکه قطر بزرگ چاه شمع تنشهای موثر عمل کننده در مقابل دیواره و کف شمع مجاور را کاهش میدهد.
تاثیر گروه برای انواع شمعها همچون شمعهای اصطکاکی درجا یا ریزشمعهای تزریق شده تحت فشار بسیار کم اهمیتتر است و حتی میتوان گفت بخاطر افزایش تنش موثر خاک ناشی از جابجایی خاک بواسطه راندن شمع یا تراکم خاک ناشی از تزریق فشاری، سودمند نیز میباشد. تاثیر گروه شمع در خاکهای دانهای نسبت به خاکهای چسبنده برجستهتر است.
سازگاری کرنشی بین اجزاء سازه
سازگاری کرنشی بین اجزاء سازهای یک ریزشمع با سیستم تقویتی مرکب بایستی در طرح سازهای شمع لحاظ شود، بویژه زمانیکه از تقویت کنندههای مقاومت بالا (مثلا آرماتورهای با تنش تسلیم بیشتر از 828 مگاپاسکال- مقاومت نهایی 1035 مگاپاسکال) استفاده میکنیم. با رسیدن به 85% تنش تسلیم میلگرد تحت فشار در مقاومت نهایی شمع (طراحی بر اساس بار ضریبدار) میتوان تنشها را از تنش مورد تحمل دوغاب، بدون ترکخوردگی و شکست فراتر برد. برای پرهیز از گسیختگی دوغاب ممکن است محدود کردن تنش تسلیم استفاده شده در طرح لازم باشد. بخش 8.16.2.3 آشتو حداکثر کرنش فشاری بتن مصرفی را “0.003” محدود میسازد، که با حداکثر تنش فولاد یعنی 600 مگاپاسکال سازگار میباشد.
معمولا سازگاری کرنشی بین دوغاب و غلاف تقویتی به دلیل مقاومت تسلیم پایین غلاف فولادی (حداکثر 551 مگاپاسکال) کمتر مرود نگرانی میباشد. همچنین دوغاب محصور شده در داخل غلاف میتواند مقادیر نش بالایی را بدون ترک خرودگی تحمل کند. سازگاری کرنشی بین یک میلگرد مقاومت بالا و غلاف باید مورد بررسی قرار گیرد. معمولا سطح مقطع غلاف بزرگتر از سطح مقطع میلگرد مقومت بالا میباشد. این امر منتج به توزیع بخش عمدهای از بار شمع به غلاف میشود. با رسیدن به 85% تنش تسلیم میلگرد در مقاومت نهایی شمع (طراحی بر اساس بار ضریبدار) ممکن است در نتیجه گسیختگی غلاف کرنشهایی رخ دهد که تمامیت اتصالات آجدار غلاف را مختل کند. به طور خلاصه، سازگاری کرنشی دلالت بر استفاده از غلاف و میلگردهای تقویتی با تنش تسلیم پایین دارد، و در شرایط تنش فشاری برای مد نظر قرار دادن سازگاری کرنش دوغاب و بخش غلاف شده شمع، این مقادیر نباید از 600 مگاپاسکال فراتر رود. در طراحی بخش غلاف نشده شمع نیز، تنش تسلیم میلگردهای تقویتی تحت شرایط فشاری، نبایستی از 600 مگاپاسکال تجاوز نماید.هدف این است که روش سازگاری کرنش، تبدیل به روشی بسیار ساده و کاربردی در طراحیهای معمول گردد. اگر کرنش ناشی از بارهای اعمالی به گونهای باشد که بدانیم تغییرشکلهای دائمی در اتصالات آجدار غلاف رخ نمیدهد.، میتوان از میلگرد با تنش تسلیم بالاتر (مقاومت کششی نهایی بالاتر در مقایسه با غلاف) استفاده نمود. همچنین اگر مستندات تهیه شده نشان دهد که دوغاب بدون غلاف میتواند کرنشهای بزرگتر از “0.003” را تحمل کند، میتوان از ظرفیت فشاری نهایی بالاتری برای بخش غلاف شده استفاده نمود.
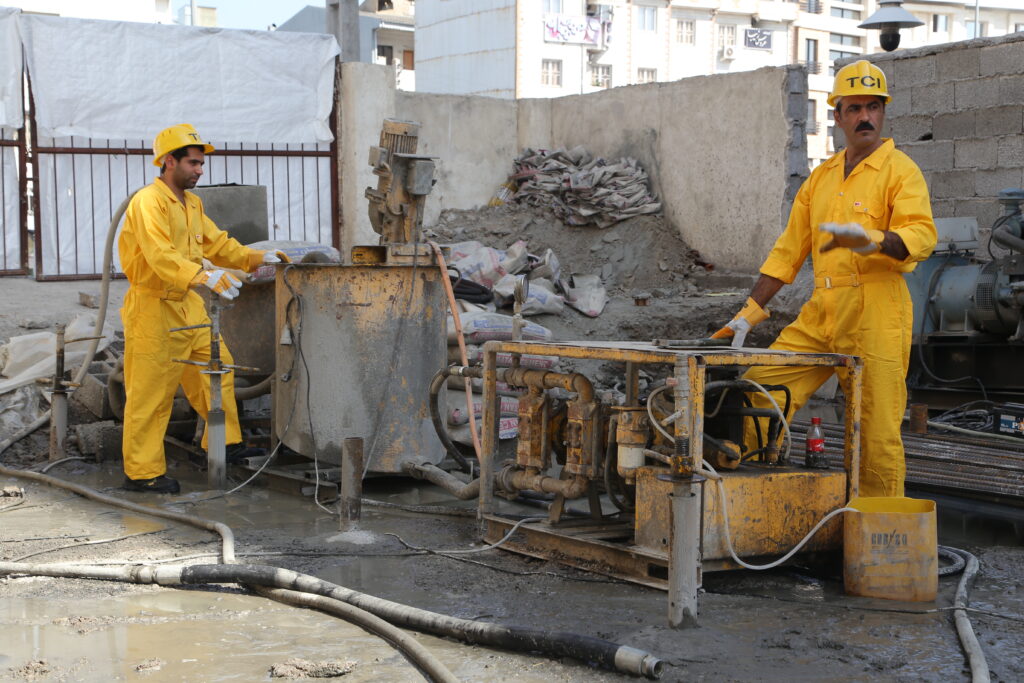
ثبت ديدگاه